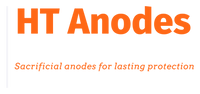

INDUSTRY
APPLICATIONS
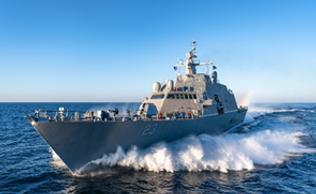


Sacrificial anodes are the principal factor in corrosion prevention. Therefore, there is a wide range of commercial use for sacrificial (galvanic) anodes due to the need to protect everyday use steel from corrosion. From the protection of offshore oil platforms and underground gas pipelines to the hulls from various sea vessels and storage tanks,
Sacrificial anode configurations for offshore structures are many and varied. Structural anodes may be flush mounted, with bar steel inserts or may be standoff types, generally with tubular steel inserts which may be reinforced with concentric or long elbow reducers to meet structural design requirements of a given anode location. Pipeline anodes in bracelet form may be paired half shells or segmented anode assemblies. Bracelet anodes may be square ended or tapered, and with a variety of mounting arrangements incorporated into the insert design. Anodes are cast around steel inserts or cores which support the anodic material, allow attachment to the structure or pipeline and provide an electrically continuous path from the structure to the anode surface. Some industry applications are:
-
Offshore Windfarms
-
Marine Vessels
-
Military Facilities
-
Bridges
-
Offshore Structures
-
Oil and Gas
-
Pipelines
-
Refineries
-
Energy
-
Electric Power
-
Water and Waste Water
-
Water Heaters and Boilers
-
Above and Underground Storage Tanks
-
Chemical Processing
-
Utilities
-
Concrete
INDUCTION FURNACES
VS
GAS FURNACES

1 2 3 4
1. Anode Melted by Electromagnetic Induction Technology (Our Anodes)
Completed lifetime anode
100% worn-out material
0% non-useful material
2. Completed Lifetime Anode
90% worn-out material
3. Anode Melted by Gas Furnace
Completed lifetime Anode
59% worn-out material
41% non-useful material
4. Non-Installed Anode
ZINC ANODES
For Marine Applications
Zinc Anodes are produced in alloy meeting U.S. Navy MIL-A-18001 and ASTM B418-73, Type 1.
Typical uses in seawater or saline mud including:
-
Hulls of ships, Barges, Tugs and Boats
-
Ballast Tanks
-
Bulkheads
-
Piers
-
Submarine Pipelines
-
Heat Exchanges
-
Traveling Screens
From Raw Materials to Packed Products in our Facility:
-
Die Manufacturing
-
ISO 19001 Accredited
-
Quality Control
-
Optical Emission Spectrometer
-
Assemble and Packing of Anodes
-
We ship to anywhere in the world


01
QUALITY CONTROL
-
In-house state-of-the-art Laboratory equipped with a Bruker-Quantron Magellan Q8 spectometer.
-
All raw materials are inspected and tested upon arrival prior to release for production.
-
Chemical results verified against MTR's.
-
Electrochemical properties performed on every batch according to NACE TM-0190.
-
Rigorous Inspection and Testing Points.
-
Scheduled equipment calibration per OEM.


02
ANODES GUARANTEE


-
Homogeneous alloys always conforming to exact international quality standards and specifications. NACE SP-0387 & SP-0492, DNV RP B401, ISO 155589-2, NORSOK M-503.
-
Our Anodes are made using only raw materials of the highest purity certifying superior electrochemical and chemical properties.
-
Our team of professional engineers, manufacturing and sales personnel are committed to provide the best quality products and excellent customer service.
-
We never melt scrap metal or recycle anodic material for our Anodes.
03
ADVANTAGES

-
Our process guarantees 100% homogeneous alloy with exceptional purity of its electrochemical composition.
-
Controlled temperature melting process.
-
This process has identical results.
-
Consistent batches and final product every time.
-
Heat is produced instantly and within the metal being melted.
-
Our process has no flames and there is no touching the material to be heated.
-
Faster Cycle Times.
FREE OF HYDROGEN & CARBON BUBBLES POROSITY
-
Favorable working conditions.
-
Surrounding area or environment doesn't heat up.
ENVIRONMENTALLY FRIENDLY
-
Clean and odorless heating process.
-
No harmful emissions or noise.
-
No polluting fuel or burners.
ENERGY EFFICIENT
-
Power is on only when being utilized.
REDUCED METAL LOSS
-
Better product yield.
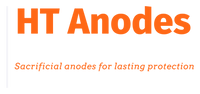
I'm a paragraph. Click here to add your own text and edit me. It's easy.
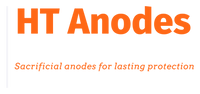